Steelmaking is an important part of our global industries. However, the process by which we make steel is extremely bad for the climate, with the byproducts of the process accounting for roughly seven to nine percent of humanity’s greenhouse gas emissions. That’s why former scientists from MIT created a company to come up with a better way that relies on electric steelmaking instead.
The scientists, who all graduated from MIT and even used MIT research to create the new method, formed Boston Metal, a company seeking to clean up the steelmaking industry by moving away from the standard blast furnace method that utilizes coal. Instead, they use an electrochemical process to eliminate several steps within the process.
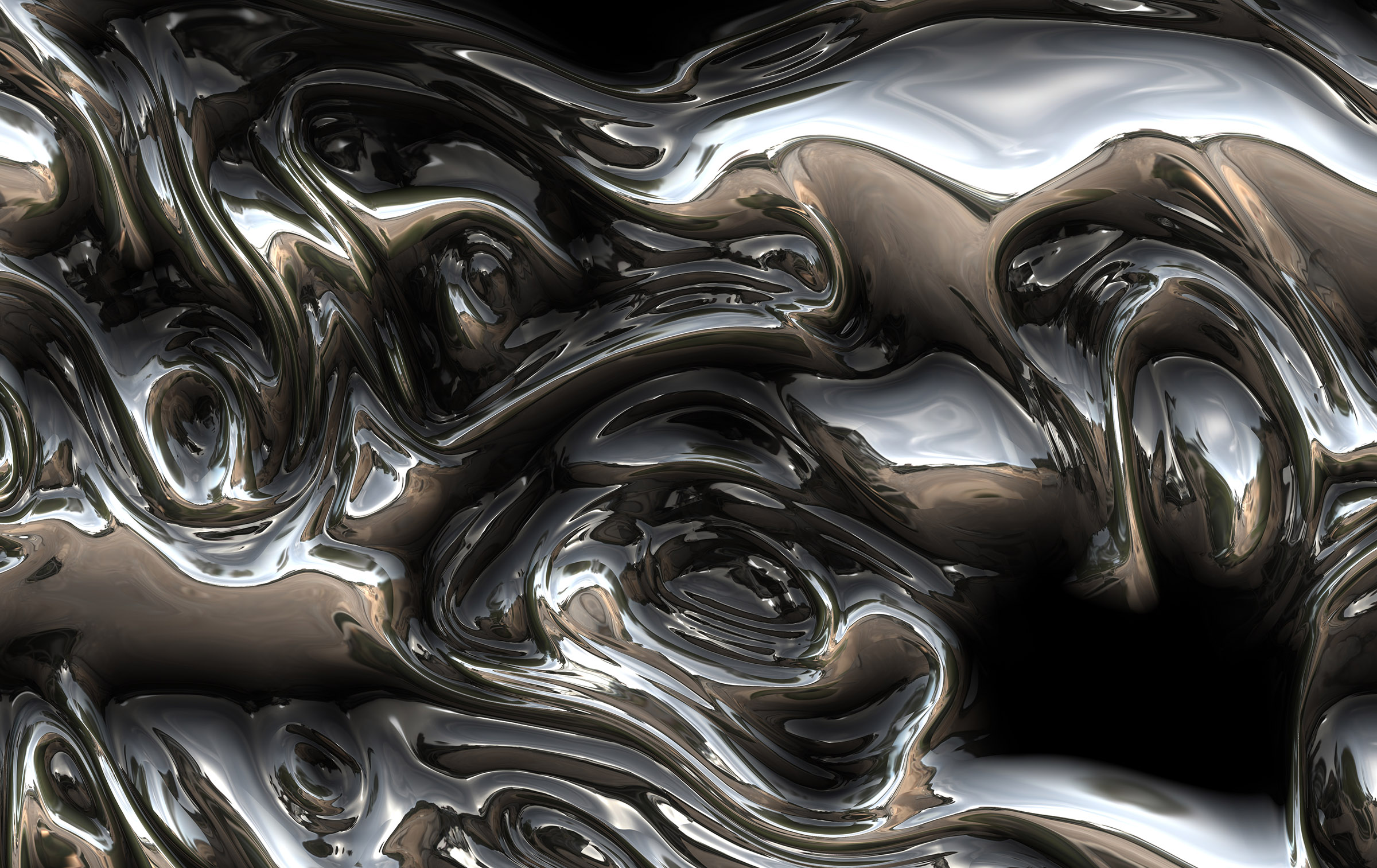
The best part of the new electric steelmaking process, though, is it only releases oxygen as a byproduct. This means it would drastically cut back on the amount of greenhouse gas emissions that steelmaking causes, and because it is scaleable to a commercial level, it could actually make a difference in the fight against climate change.
Researchers have been looking for a way to use an electrochemical process to push steelmaking for years. However, it has never been scaleable to a commercial level. That changes with the new technique that Boston Metal relies on. As the company explains in a paper published in 2013, the process utilizes modular molten oxide electrolysis cells.
From there, it relies on a specific iron anode that is inert and doesn’t dissolve when completely immersed in the liquid electrolyte. This inertness is what allows the electric steelmaking process to actually work, as the anode can then have electricity run through it, causing the iron oxide bonds in the ore to split and thus turn into pure liquid metal.
The current technique is estimated to reach commercial scale in 2026, though a factory in Brazil is already using the MOE process.